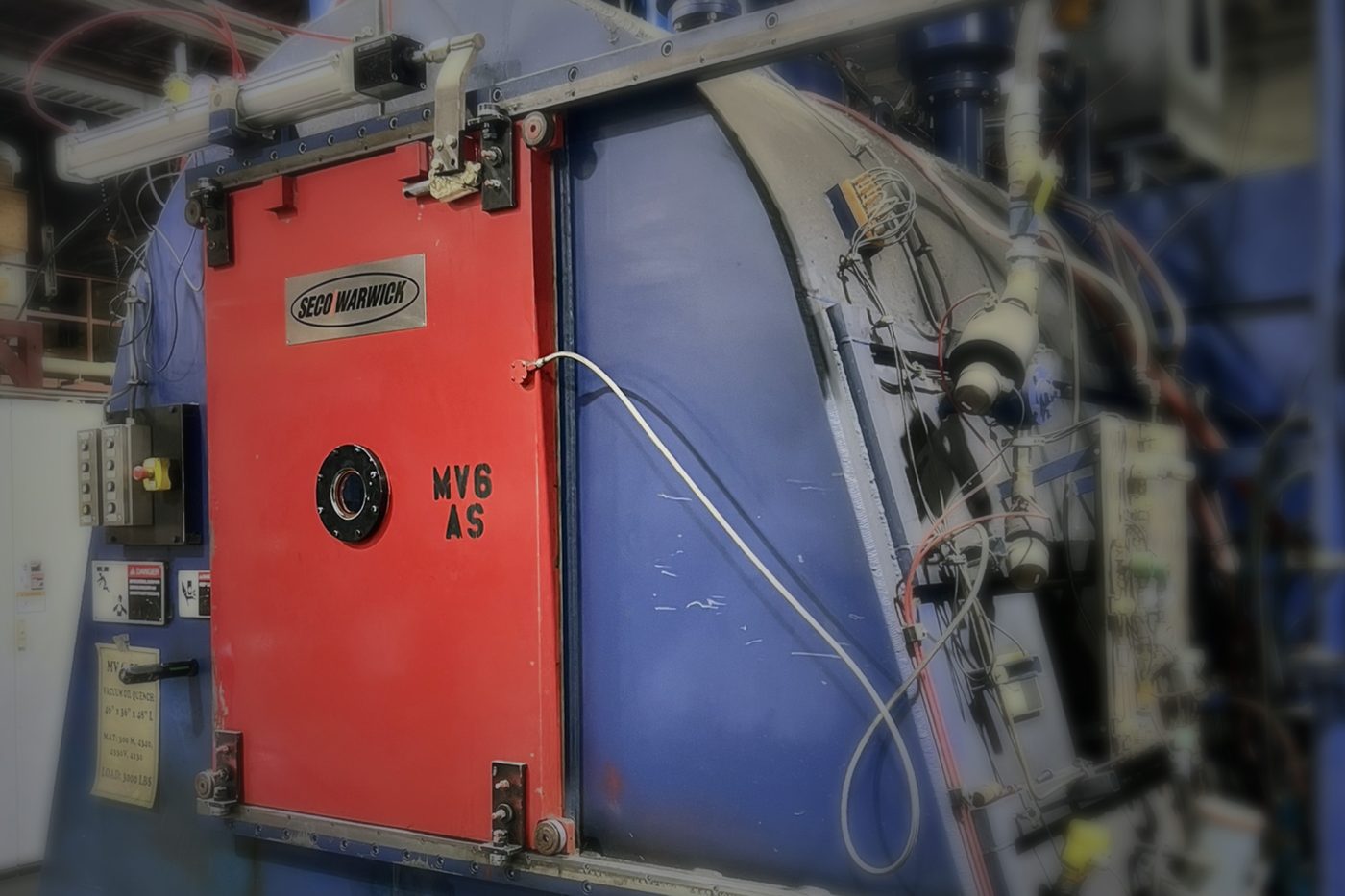
Expert Services for Superior Performance
Enhancing material strength and longevity with advanced heat treatment technologies. Trust our expertise to deliver customized heat treatment services tailored to meet your specific industry needs.
Our Heat Treatment Services
Get in touch for your quote today!
Simply fill out our easy-to-use form, and our experts will provide you with a free no-obligation quote tailored to your specific requirements!